In a fight to reduce emissions in the automotive industry – aluminium is the winner. Here is why
Light-weighting with aluminium is one of the most effective ways to improve the energy efficiency of electrical and hybrid vehicles.
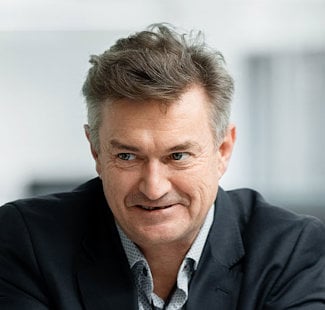
What is the future of the automotive and transport industry? Although there are plenty of uncertainties, one thing is certain: Driven by increasingly restrictive regulation to combat carbon emissions and improve air quality with emission-free driving, the future is clearly going in the direction of e-mobility, or electric vehicles (EVs).
Aluminium decarbonizes transport
For over 40 years, there has been continuous growth in the use of aluminium in the automotive industry. This is due to its light weight, alloy strength, corrosion resistance, and, last but not least, its processing possibilities.
In recent years, the light-weighting trend has accelerated due to increasingly tough measures to curb exhaust emissions, as well as the fact that cars have been getting heavier overall on the back of increasing demand for larger models packed with extras.
The automotive industry is continuously striving towards lighter constructions – particularly in EVs. Lighter cars need less electricity and fewer or smaller batteries to travel the same distances.
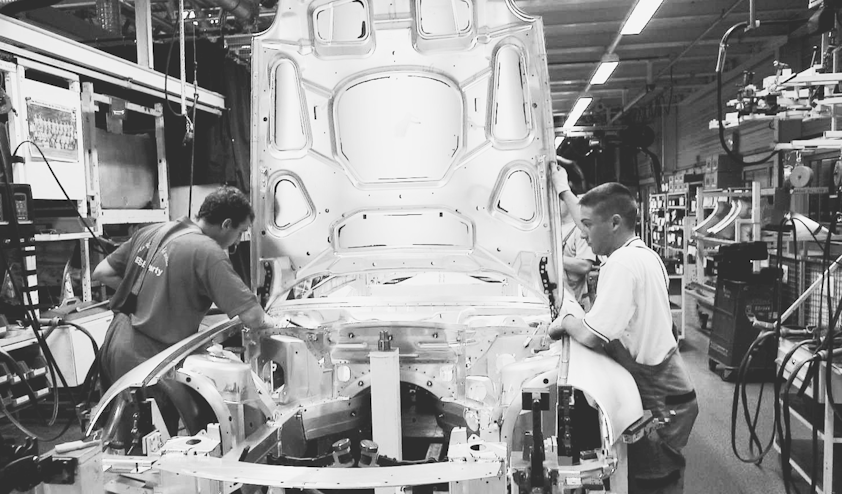
CO2 footprint and total life cycle of vehicles
Furthermore, in the face of increasing regulation and climate concern, there is more focus on the CO2 footprint of vehicles from a total life-cycle assessment (LCA) perspective.
As emissions from the use phase are driven down, the relative importance of the build phase naturally increases. Hence it is expected that both governments and Original Equipment Manufacturers (OEMs) will start to focus on the CO2 footprint of the materials used, and that this will underpin the materials selection process.
So, moving from selecting materials based mainly on cost and properties, in the future the assessment will be based on cost, performance and the embedded CO2 footprint from raw materials extraction and production.
This effect is especially prominent for EVs. If the vehicle is driven on renewable electricity, the life cycle emissions of a vehicle will stem almost entirely from the embedded carbon in the materials used to produce the vehicle. Considering the lifecycle emissions of vehicles thus represents an enormous opportunity in materials innovation.
Aluminium products with net-zero emissions
The automotive industry is shifting its emission reduction focus from the use phase to the embedded emissions in the materials and the supply chain.
Aluminium is a key enabler in the green transition, due to its exceptional properties. However, production is energy intensive, and the global embedded carbon footprint (Scope 1 and 2) is thus at approximately 16.7 kg CO2 per kg aluminium.
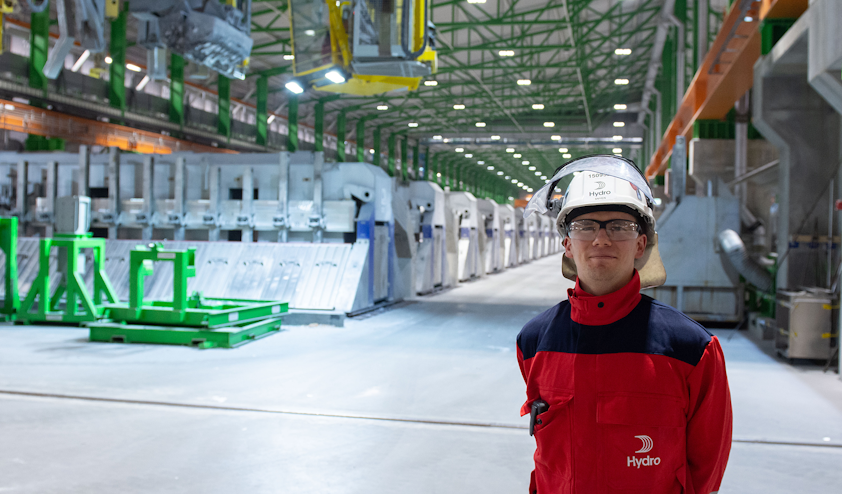
In Hydro, reducing CO2 emissions has been a focus area for decades and we have made great strides cutting the embedded CO2 footprint in our products by 70% at our fully owned smelters since 1990. Using renewable energy, best available technology and highly skilled operators, Hydro today produces Hydro REDUXA with a carbon footprint less than 25% of the global average and guarantees a footprint of 4 kg CO2 per kg aluminium.
Over time, however, aluminium production must become emission free – and Hydro will take the lead to get there. Hydro’s ambition is to deliver aluminium with near-zero emission already in 2022, to take the lead in delivering industrial scale zero-carbon aluminium by 2030 with the aim of converting our entire portfolio to achieve net-zero emissions by 2050 or earlier. Our efforts are concentrated along these main pathways to zero:
- Recycling of post-consumer scrap with decarbonized operations
- Carbon capture and storage for existing smelters (CCS)
- Development of Hydro’s proprietary HalZero technology for greenfield smelters
Greener aluminium lowers emissions
When using greener materials such as low-carbon aluminium, the footprint of an electric vehicle will be improved, not only in the production of the vehicle, but in its use phase. With the move to electrification, the materials footprint of a car will soon be more important than the tailpipe emissions.
Sustainability is one of the drivers for choosing electric vehicles. That is why Hydro is developing materials and production techniques, to ensure our automotive customers receive the aluminium they need to meet their sustainability targets.