Steve Buechi: One of the experts helping shape Hydro’s recycling growth journey
Hydro’s milestone near-zero aluminium production at Clervaux, Luxembourg, in 2022 was accomplished thanks to years of innovation, learning and improving. This is the story of how Steve Buechi became an adventurer and made history in Hydro.
“The world needs a green transition to fight climate change. This is both our most important challenge and our biggest opportunity. The world must reduce its carbon emissions and I am excited to announce Hydro’s ambition to deliver the first commercial volumes of near-zero carbon aluminium already in 2022,” said President and CEO Hilde Merete Aasheim when the company launched its new sustainability ambitions December 13, 2021.
How would the company produce near-zero aluminium? This is a feat never achieved before in the aluminium industry. It is considered a milestone needed to meet the demands of increasingly climate conscious consumers and important contributors to the ambitious targets imposed by European regulators.
On May 10, 2022, five months later, Hydro announced its recycling plant in Clervaux, Luxembourg, had produced 130 tonnes of near-zero carbon aluminium with 100 percent post-consumer aluminium scrap. The production milestone was a significant improvement, compared with the current 2.3 kg CO2/kg aluminium in Hydro CIRCAL extrusion ingot with 75 percent post-consumer aluminium scrap. The use of post-consumer scrap significantly reduces the CO2 footprint compared to pre-consumer/process scrap as well as primary aluminium.
The team in Clervaux knew the degree of difficulty, precision and process control that is needed to make a spearhead product such as near-zero aluminium. Steve Buechi, a Hydro employee since 1998, was one of the key operators given the responsibility to overlook the final quality control of the milestone production.
Steve’s life story reveals he could have ended up anywhere else in the world than at the recycling plant in Clervaux. As we meet him inside the plant, his bright smile, coolness and calmness gives an indication to a remarkable human being that has seen it all.

This is the story of Steve’s journey in life and in Hydro, and how a meeting with an “American coalition” turned out to be the start of an incredible career and personal growth journey.
“From time to time I think about the fact that I was only meant to replace someone that was on sick leave in 1998. Well, look how that turned out,” says Steve.
An adventurer destined to travel the world
Steve’s father, a Swiss American, moved from the United States to Luxembourg to work at Goodyear, one of the world’s largest tire companies, and their new production site. This is where he met Steve’s mother and where Steve was born in 1966.
“We moved to many different places because my father did well and got many different international assignments. We lived in the Republic of Zaire, Bangkok, France, the United States, Germany, then back again to Africa, this time to the Democratic Republic of Congo. We basically moved all around the world and this became a way of life for me,” says Steve.

“My first language was English, but I also quickly learned Swiss and German, and when I eventually moved back to Luxembourg, I learned French. It was a wonderful experience to see the world and learn about different cultures and meet so many people. However, the frequent moving meant that I was switching between school systems and practices, so it became difficult to keep up at a certain point.”
Returning home
When Steve became 18 years of age, his family decided to move back to the city of Clervaux after almost 20 years travelling the world. He was unsure of what to do next and what to do with his life.
“Most of my friends went to the university, whereas I was a bit tired of school and education, and wanted to get some job experience before figuring out what I wanted to do. I got a job in the Luxembourg public administration office where I did a lot of basic administrative work. I had very nice colleagues, but the work became a bit boring at one point,” Steve says.
“I started reflecting more and more about who I really was. I had already seen most of the world and been travelling for so long, I guess I wanted a stable job, but also one where I saw clear purpose, contributing to something bigger than myself,” continues Steve.
Clervaux is a small town in Luxembourg, where most people know each other and have many of the same meeting arenas. Steve also lived close to the Hydro recycling plant where one of his friends worked.
“We had a conversation and he told me that I should come work for Hydro. I got an opportunity to work temporarily as a contractor for three months to replace someone that was on sick leave. My English skills became key for landing the opportunity,” Steve said.

From administration to operations
Steve enjoyed the work, but it become apparent very quickly that working in operations was a totally different challenge than working in administration.
“At first, I was a bit scared. Not only was everything new, but everything was so big, hot and loud, you do not understand what is going on, and it was difficult to understand the process,” he says.

“I decided to take that early challenge head on. I got engaged and started to ask more questions, listen to my colleagues so I could learn more and asked for more responsibility. It also helped I knew some people from before, which gave me motivation to fight and be really interested to learn more. Eventually it ended up with me getting extra work at the shift I was in,” Steve remembers.
Time flew by and Steve’s assignment was ending, but when the time came for him to turn in his helmet and workwear, the company said they wanted to keep him and offered him a full time job.
“Normally, I would finish after three months, but they wanted to keep me. I took the job offer because it was fun and interesting. I fell in love with the industry and the company, and decided this was a good place for me. I felt more or less in balance and wanted to keep it that way,” says Steve.
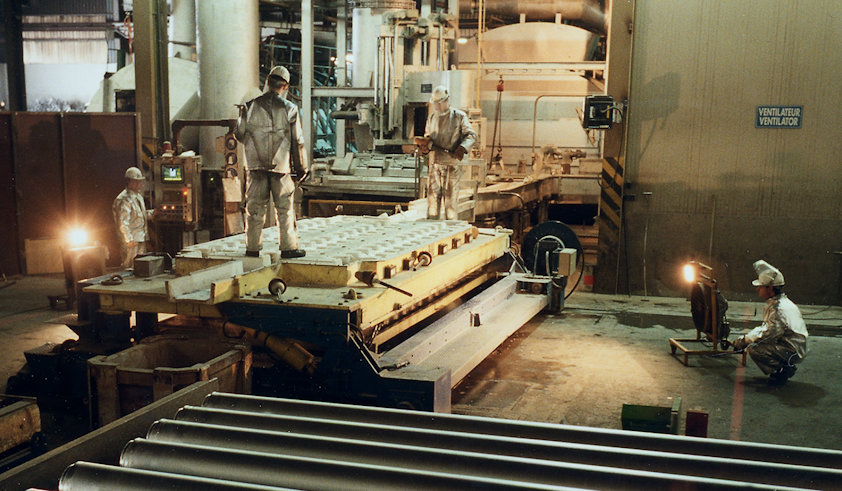
An American coalition that would change everything
One day in the late 1990s Steve was invited to a dinner with some of his coworkers, when a Hydro team from Norway and a large group of Americans came to Clervaux.
“It was a nice dinner. We started talking, and since my English was good and I knew the American culture after living in the US, we hit it off,” Steve recalls.
Little did he know that the dinner would prove to be decisive in sending him off to his next adventure.
Hydro expanding into Henderson, KY to build its first recycler in the U.S.
A couple of months after the dinner in June 1999, Hydro announced it would build the company’s first aluminium recycling plant in the U.S. to produce aluminium billets. The facility would be built in Henderson, Kentucky, which is considered by some a “second Detroit” in the U.S. automotive market. The USD 33 million investment would employ about 45 people and produce about 90,000 tons of billet a year. At the time, the total North American open market for billet sales was slightly more than one million tons a year.
Steve did not know it, but the American coalition that came to Clervaux for dinner was putting together a team of experts to train and prepare the 45 employees that would eventually run the Henderson plant.
They were so impressed by Steve’s language skills, his demeanor and personality, they called him and asked him if he could be part of the start up team of experts. The role of the expert team was to be responsible not only to train the operators and employees, but also to run the plant for the first weeks and months.
“I knew and liked the American mentality, so I decided ‘why not’ and went for it. Even though I was a bit sad to leave my colleagues, I said yes without hesitation. In a way, it was a call to my younger self, and I guess the opportunity lit a fire in the adventurer I had once been,” said Steve.

“It felt like an amazing opportunity for me and I was very proud to be asked. It meant I had done something right in Clervaux,” Steve said. He packed his bags and moved to Kentucky to take part in Hydro’s recycling story.
A strategic approach to build a stronger position within remelting and recycling
The greenfield development in Henderson was part of a strategic approach to offer remelting services for process scrap to customers, basically leftovers from the aluminium production process, and to take a stronger position in the recycling of aluminium. The building of the network of casthouses started with the acquisition of Clervaux in 1995, followed by Hydro Rackwitz in Germany in 1998, and Hydro Deeside, located in Wrexham, Wales in 2000.
At the same time, Hydro was also identifying interesting spots to build greenfield plants.
This is how it was decided to invest in building greenfield plants in Henderson KY, Azuqueca, close to Madrid in Spain, and in Commerce TX.
The final piece in the puzzle in the early 2000s was the acquisition of the Lucé casthouse in France in 2001 which was acquired from one of Hydro’s business areas – Hydro Extrusions.
The rationale was simple. As with all parts of industrial production, when you produce aluminium, you have leftovers in the process, what we call “pre-consumer” or “process” scrap. So instead of throwing it away and creating more waste, Hydro takes back the leftover scrap from its customers, remelts it, and turns it into new aluminium billets. This was an important offering to customers and helped Hydro grow its sales of extrusion billets in the U.S. and European market.

In short, Hydro saw the recycling or remelting aspect as a business opportunity, but also as a way of keeping the metal in the loop, which is better for the environmental footprint.
Touchdown in Henderson
In other words, the Henderson greenfield plant was a particular and important part of Hydro’s history to take a larger part in the transition to a more circular economy, both in Europe and in the U.S.
When Steve speaks about this and the Henderson project’s place in Hydro’s recycling history, he reminiscences about feeling the pressure to do things the right way. When building a plant from the ground up, the challenge is to implement a solid foundation from day one and it starts with safety.
“If there is one thing I have learned in Hydro, it is that we have extremely high safety and operational standards, and it’s a mindset that needs to be implemented from day one,” Steve said.
There is a transitional challenge when moving from one industry to a completely new one, as many of the workers at Henderson did.

“The employees and people we coached were very good people. The hardest part was to install the safety mindset, and my job was to pass on my knowledge and install this in them. The most important and difficult aspect is to understand the most immediate danger is not visual, is not there, but that it can occur at any moment. Therefore, risk awareness is critical because you could be dead or injured for life if you do not understand the risks. From there on, we built slowly, layer by layer. The basic work was safety and the organization,” Steve said.
The training was challenging, but steadily progressing.
“It’s also about some basic, but important business systems and how to work efficiently. In essence, what we try to do in our industrial processes is to standardize our procedures and work continuously to improve them to eliminate waste, pursuing the most efficient methods. This results in people returning home safe, but also in high quality products,” Steve said.
The project was not only a learning process for the employees, but also the expert team.
“A completely new plant is not only giving input to people, but there is an overall learning process for yourself. The layout of the plant was different to Clervaux, the machines and equipment are different. So, for the experts, it was also a learning process,” Steve says.
It took some time to do the work, but the Henderson plant started normal production and functioning after a year.

Steve then went back to Clervaux, filled with more experiences to bring back to his plant.
“I really enjoyed the experience. Obviously, it was a tremendous challenge, but we did it and it was good to come home,” Steve said.
A short stop in Clervaux before Uncle Sam came calling again
Shortly after Steve had returned to Clervaux and his “home” plant, news emerged in September 2001 that Hydro was going to build another recycling plant in the U.S., this time in Commerce, Texas, with the company looking to strengthen their commitment to expand their recycling capacity in the United States.
The Henderson plant had been operational for approximately six months and had already received successful feedback from customers on the product quality, which made Hydro confident they could achieve the same level in Commerce.
“I think this was a proud moment for the team of experts, but also the whole Henderson organization that we had done what we set out to do. The Commerce investment was a true example that the commitment and dedication we put into it was worthwhile, and had given results,” Steve said.

As with Henderson, Steve and other Hydro employees were once again called upon to join the expert team charged with the responsibility to prepare, train and implement the right mentality and procedures with 40 new members of the Hydro family.
“I did not hesitate when I got the chance to go back to the U.S. I thrived in that culture, people were so friendly, and we all became like a second family,” Steve said. “Commerce went smoother because of the experience from Henderson. We had a plan and structure in place, so it was easier to keep track of things, and we used that momentum to be even better in our preparations and training.”

When the state of the art recycling plant in Commerce was operational in 2002, Hydro had either built or acquired seven recycling plants in Luxembourg, Germany, UK, Spain, France and the U.S. since 1996.
“I think the foundation that was built during those years gave our company a solid platform that we see the benefits of today. In my view, the company showed foresight to take those steps in the late 1990s, not only making money, but also combining the sustainability aspect. I am very proud to have been part of that journey,” Steve says.
Steve returned to Clervaux, where he continued his work as shift leader and operator. He enjoyed life and work at the recycling plant, moving between different units and shifts, learning and growing.
Qatalum
In 2009, Steve would take his talents to Qatar, where Hydro was assembling the best of the best to complete a gigantic, looming project in the Mesaieed Industrial City outside Doha.
The Qatalum development is the largest Norwegian industrial project abroad, with a total investment of USD 5.7 billion. First metal was produced, on schedule, in December 2009, and the plant reached full capacity in the fourth quarter of 2010, according to plan. This was the result of more than 90 million working hours. More than 56,000 workers, from more than 200 companies, have been directly involved in the construction in Qatar.

“Qatar was different and a whole new learning experience. For one thing, I worked with a different product, foundry alloys instead of extrusion ingot, which means the procedures are different. Still, what they have in common is the prime material. Before we went to Qatar, we had training with the team at Sunndal, Norway for one week in October and one in February,” Steve said.
As many others that took part in the project will testify to, Steve was also left speechless on the scale and size of the project.
“It was a huge site and the dimensions were out of this world. By comparison, in Clervaux, we have one small production line that is difficult and complex enough in itself. In Qatar, we had five or six. The conditions outside were 45 degrees and believe me, you do not want to know how hot it was inside,” he says. “You get used to it though, and we could take a shower in the middle of the shift and change clothes.”

Being a shift leader when the lights go off
“I was working as a shift leader, and as you can imagine, things are not always working, and the process is not optimal. This is why we are there, to continuously work to find new and better ways of optimizing the process so that we can be in control and capable. One morning I came into work at 06.00 and everything was dark. I was like, what is going on? The emergency lights came on and everyone was on red alert searching for the root cause to fix it and get the power back. That is the job though. We are trained for this and it is what we are here to do,” Steve says.
The organization and management also impressed Steve.
“I had the chance to go there beforehand and meet the project organization that was constructing everything. I saw the responsibility the management had and the immense pressure they had to stick to the plan. They shared our same culture and beliefs, it was nice to see the management was so dedicated to the safety and operational excellence,” Steve explains.

“I am so, so proud to have been there and part of that project. In total, when you look back at that decade from 2000-2010, I was part of startups in Henderson, Commerce and Qatar. I will never forget it in my life. It was simply amazing and it has broadened my horizon in ways I could have never imagined.”
Digging deeper into the scrap pile and aiming higher
For the past 12 years, Steve has continued his adventures in the Clervaux recycler. However, the recycling business has completely changed. The recent near-zero production milestone he was a part of is a true testament to this. The milestone was also a result of years of research, development and strategic acquisitions.
Hydro invested in advanced sorting technology in Germany in 2015, enabling the company to go deeper into the scrap pile and recycle more post-consumer, end of life aluminium scrap. With this technology, Hydro had the necessary capabilities to “upgrade” the scrap. The sorting capability led to other upgrades, such as technology developments in the recycling furnaces, enabling them to deal with more advanced scrap types.

“The new scrap types we get in and work with is of course on another level. We must stay relevant in the market and in the world around us. For us as operators, we also need to learn and adapt in order to meet customer demands,” he says. “We see the sustainability shift everywhere. We see it on the raw material we use, but also physically the stack of our greener products piling up and are gone the next day. We have many meetings to discuss potential product areas and so on. There is a constant evolution.”
Steve’s main job today is to ensure the quality of the products before they get to the customers and puts all the emphasis on the entire team in Clervaux.

“This is teamwork and organization work. We cannot have any bottle necks, so we all need to work together. From the scrap buyers, management, safety, quality, the packing station and out to the customers. When the products do come to our table, we will be ready. Our customers should not wait,” he says.
Responsibility to improve
“Here in Clervaux we have nine nationalities and speak a total of 11 languages, but regularly only five. His experience from his travels early in life and later in Hydro, means he can easily interact with anyone. Like many of our employees, he has work experience from outside of Hydro, so that brings an important outside in perspective. He has been instrumental in the near-zero aluminium production milestone and will be in the future to keep working to improve and evolve as a company,” says Ludovic Dardinier, Managing Director of Hydro Clervaux.

Steve speaks highly of the relationship between management and operators on the shop floor.
“There is a good culture here for involvement and collaboration, which is key. Involvement creates engagement, which leads to innovation. We are out there every day and are therefore responsible for improving a plant with safety, efficiency and predictability,” Steve says.
“I see it with my own eyes. If I am on leave or vacation for more than two to three weeks, I like to go abroad. But when I come back, the plant is not the same as it was when I left. Because of innovation and continuous improvement, something has changed for the better. There is always an evolution, big or small, whenever I come back. That is down to all the input which we, the operators, give to the management at Clervaux, which can then be implemented if applicable and relevant on a companywide level, it could be in the U.S. or in Norway. I saw just that in Henderson, how the plant structure, process and design was in constant evolution because of input from other parts of the company,” he says.
It is important to be curious and engaged, especially when you are at the beginning of a job and know very little.
“I see that we have an impact. That makes me loyal. I see that my view, my input and my work is important for the development of the company. This is not propaganda, but my honest experience. It takes courage to ask for more responsibility when you know nothing, as I did when I started here. But I have seen that if someone shows interest and is willing to do the work, that is what makes the difference and will bring the company forward,” he says.

Finding his identity?
Steve says the experiences abroad made him find again and appreciate his early experiences as a child traveling the world with his family.
When asked if he has now found the identity that he set out to find when he left the job in administration, he smiles and laughs before answering.
“What is my identity? Who am I really? Maybe I am a chameleon, shaped by the adventures and travels I’ve been fortunate to have as a kid, in private, but also now in Hydro. The one thing that has stayed consistent since is that I have been travelling the world, but I still haven’t seen everything, so who knows what and where my next adventure will be,” he smiles.

It was only fitting then, that when Ingrid Guddal, the newly appointed Head of Recycling, came to Clervaux to learn, Steve was one of the key people she talked to and learned from. After all, she headed the local startup team in the recycling plant Azuqueca, Spain in 2001 before being appointed plant manager for the plant in 2007.
Needless to say, they had a lot of common experiences.
In Ingrid’s new role, she will oversee the strategy and direction for all the recycling plants, including Hydro’s next state of the art aluminium recycling plant in Cassopolis, Michigan. The plant will strengthen Hydro’s ability to supply car makers and other industries in the U.S. with recycled aluminum.
The project is on track for startup during the second half of 2023 and is looking to establish an expert startup team to lead the training and development of 70 new employees.
Maybe they need an expert?
