
Aluminium for crash management applications
Automotive crash management systems and associated parts are crucial for driver and passenger safety in high speed crash environments. They are also important for ease-of-repair after low-speed crashes, and in reducing the costs associated with damage.
Their role is to meet stringent energy-absorption requirements resulting from vehicle-level crash obligations in the event of front collisions, while complying with design, weight and durability requirements.
Aluminium extrusions offer unparalleled design flexibility, which in combination with a unique automotive alloy portfolio and advanced fabrication capabilities, provide a straightforward path to designing high-performance crash management systems (CMS).
To achieve the highest performance and the best performance-to-cost ratio, it is important that you engage with Hydro's extrusion teams at an early stage, with functional design targets the key. This will allow alloy selection, extrusion design and fabrication suggestions to be made during feasibility rounds.
Common crash management system applications for aluminium extrusions
We offer a fully integrated value chain of casting/recycling and extrusion, complemented with advanced manufacturing, including passivation, bending, forming, stamping, welding and machining. This enables us to successfully serve the most demanding OEMs with the following CMS parts:
• Front bumper beams
• Rear bumper beams
• Crash boxes
• Longitudinal beams
High-strength aluminium and automotive crash alloys
Crash-relevant parts are divided into two categories, those aiming at absorbing energy under axial crush loads such as crash boxes (crash optimized) and those aiming at transferring forces resulting from axial crush loads such as bumper beams (strength optimized).
Hydro is committed to developing aluminium alloys within our 6xxx (AlMgSi) series that are optimized for CMS-related products. These display key properties including strength, ductility and durability, while remaining suited for both extrusion and further fabrication.
Crash-optimized 6xxx alloys targeting axial crush loads are generally referred to as C-grades followed by figures highlighting the minimal yield strength guaranteed. The higher the strength, the higher the specific energy absorbed (kj/m) for any given design.
Research and product development
Hydro is continually developing low-CO2, high-performance aluminium solutions for the automotive industry. Our development programs and teams operate both internally and within automotive partnerships, to support and help develop OEM ambitions while meeting industry-specific safety regulations. This is part of our automotive DNA.
Aluminium extrusions and extrusion based components can provide the optimal manufacturing choice for CMS and crash based products. They offer both a high strength and light weight material that can display high energy absorption and is easy to form into automotive designs. Our unique alloys can also reduce the carbon footprint in the manufacturing phase and with reduced weight improve vehicle running economy.
Related pages
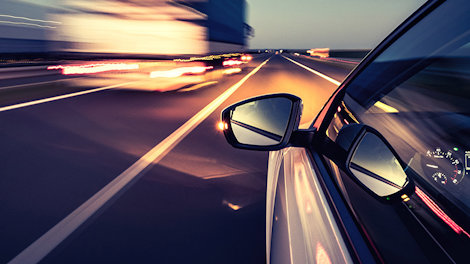
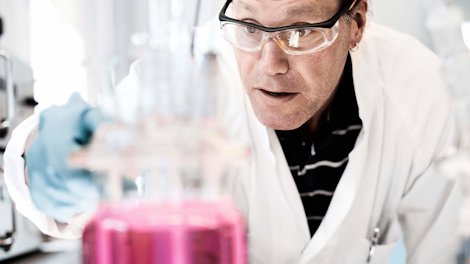



